Thermally modified wood is wood that has been modified by a controlled pyrolysis process of wood being heated (> 180 °C) in absence of oxygen inducing some chemical changes to the chemical structures of cell wall components (lignin, cellulose and hemicellulose) in the wood in order to increase its durability.
Industrial thermal modification processes typically aim at improving the biological durability of less durable wood species and enhancing the dimensional stability of the wood or wood-based products.
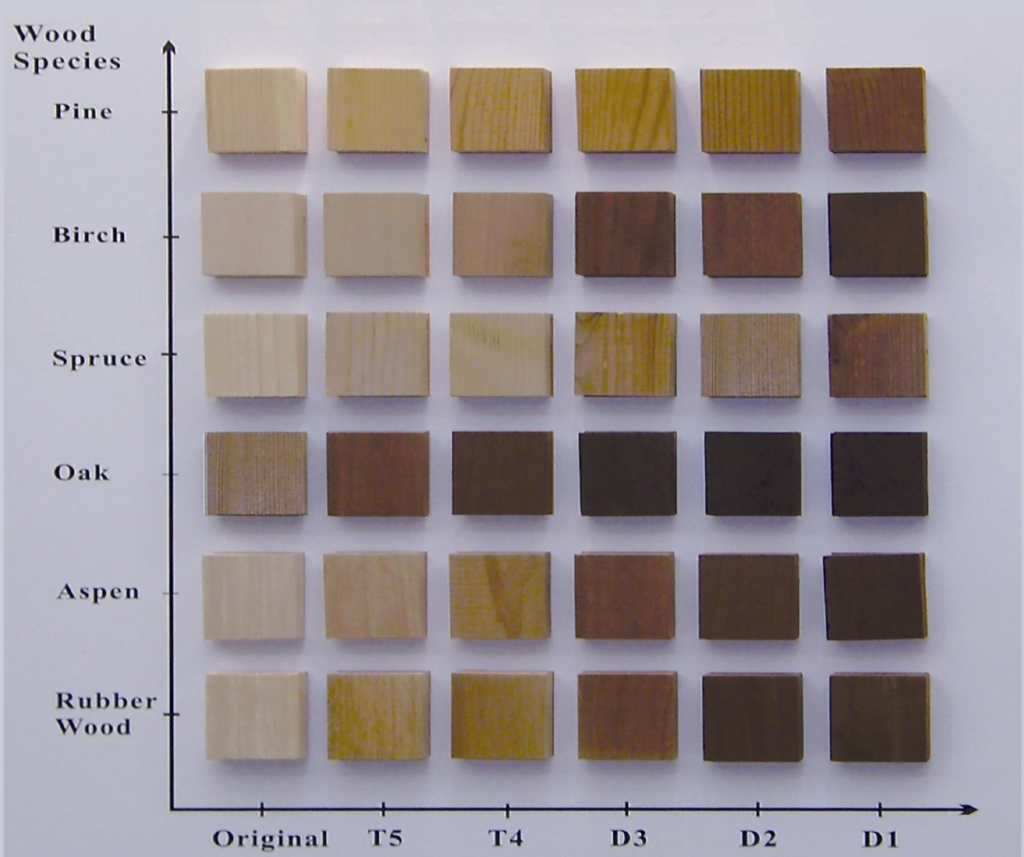
Colors of some thermally modified wood species
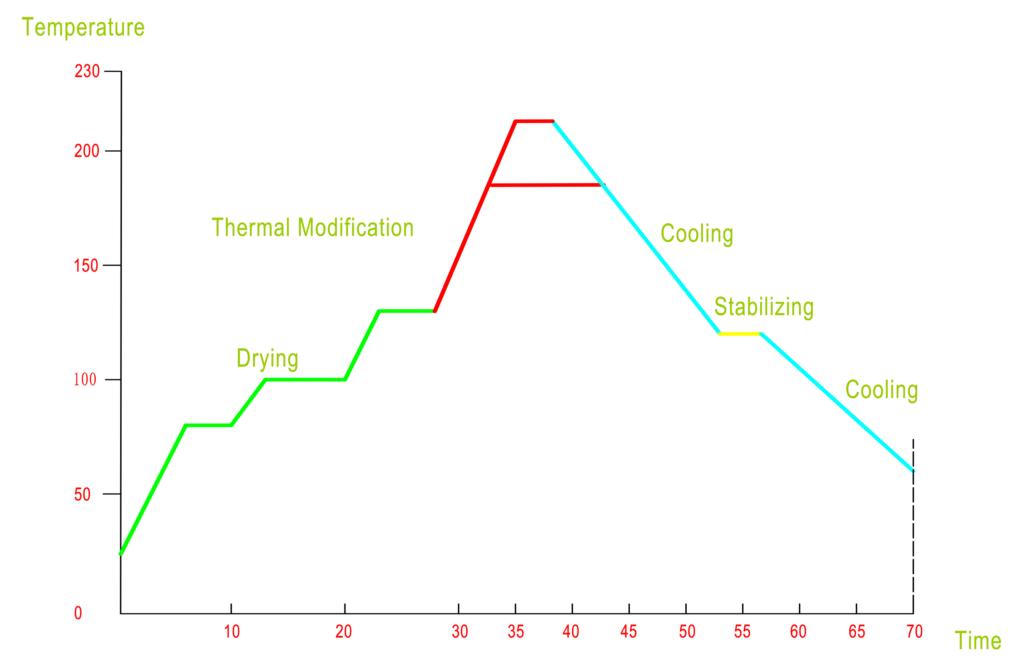
Thermal modification process demo chart
Experience the ultimate in wood treatment technology with our state-of-the-art high temperature wood thermal modification kiln. Designed for versatility and efficiency, our kiln offers dual heating options: electric heating or thermal oil boiler heating, allowing you to choose the best heat source for your needs.
Equipped with advanced PLC automatic control and an intuitive, user-friendly HMI screen, our kiln ensures seamless operation and precision. Achieve superior results with ease and elevate your wood treatment process to new heights.
Discover the difference with our cutting-edge thermal modification kiln – where innovation meets excellence.
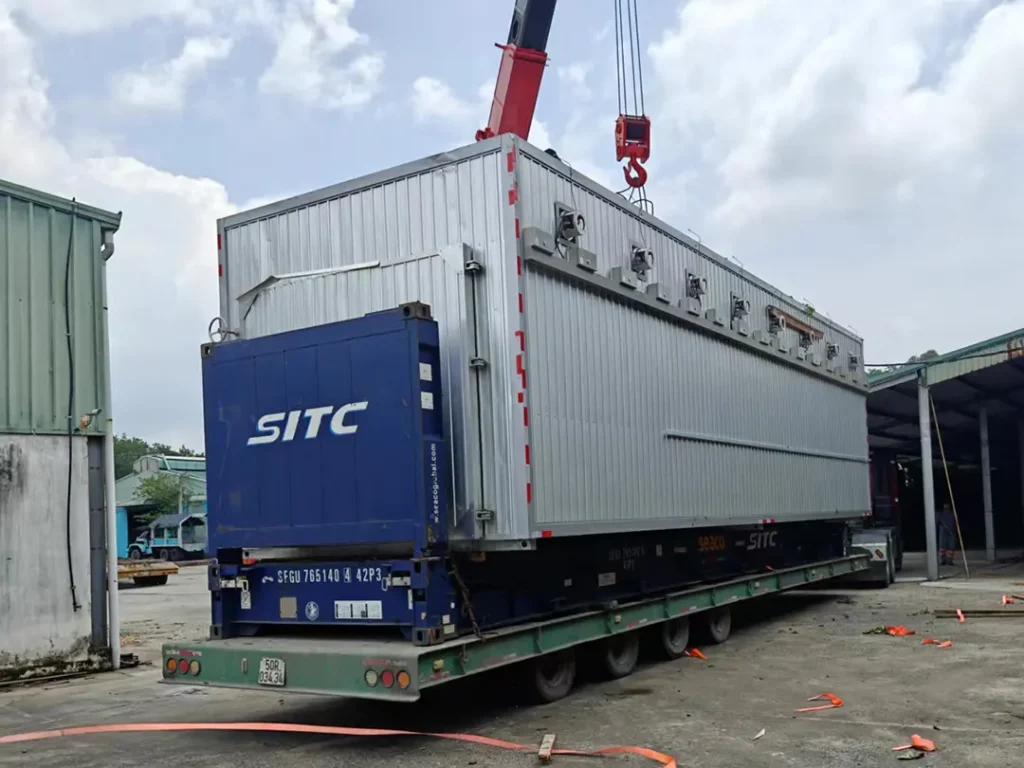
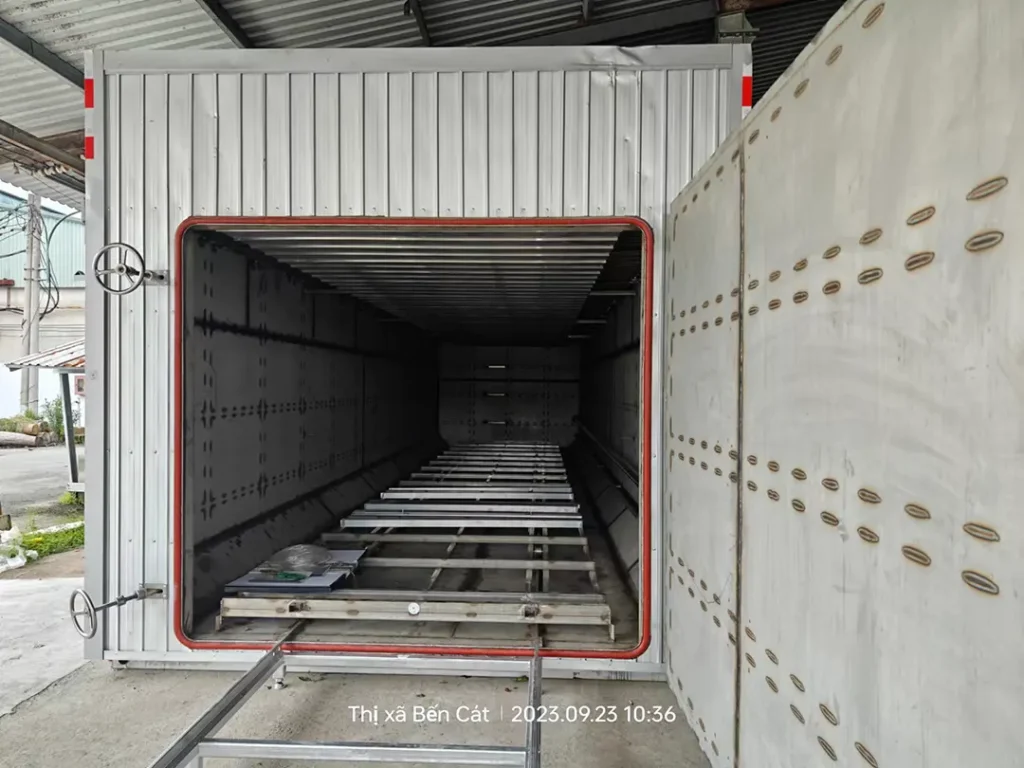


Features of thermal modification kiln
Featuring an intelligent and fully automatic operating system, easily managed by a single person.
Equipped with an independent sensor detection system, complemented by an HMI screen displaying parameters clearly.
Incorporates a multi-species benchmarking database to meet precise matching requirements.
Crafted from high-quality special raw materials, ensuring a robust and durable main body for the equipment.
Boasts a special structural design and development, simplifying tasks and conserving energy.
Allows customization of the heat source and working volume based on site conditions.
The entire working process is physical, without the use of any chemical additives, ensuring the wood remains purely natural and environmentally friendly.
Enables real-time observation of the timber color to achieve perfection.
Equipped with a safety alarm system to swiftly and effectively prevent and eliminate potential hazards.
Benefits of thermal modification kiln
Deep Treatment
High-Temperature
Patents
Transfers temperature to deeper layers, ensuring comprehensive treatment beyond the surface.
Physically enhances wood stability, minimizing susceptibility to cracking and warping.
Boasts more than 20 patents for intellectual property and technology.
Ease of Processing
Physical Effects
Aesthetically Pleasing
High-temperature treatment facilitates easier sanding, grinding, carving, and cutting.
Achieves complete degreasing, desugarization, degumming, insecticidal, and anti-termite properties.
Simple, gorgeous, uniform, and adjustable in depth.
Green
Weather Resistant
Professional Presentation
Chemical additive-free, low carbon, purely physical treatment.
Enhances wood’s weather resistance, providing physical resistance to mold and decay.
Comprehensive services from design and production to installation, training, and after-sales support by a dedicated team of professionals.
Indoor & Outdoor
Unique Process
Color Control
Suitable for both indoor and outdoor applications.
Direct thermal modification of wet coniferous timber.
Real-time observation of the modification process and status.
Intelligent Control
Slackness
Woods Loading
Offers automatic, remote, and HMI control.
Door adjustment available during operation.
Motor drived loading & unloading.
Temperature Setting
Effective Volume
Applications
Adjustable based on the specific density and requirements of different wood species.
From 1 to 120 cubic meters.
Suitable for all solid wood products, plywoods, wooden boards.
Model | ETM-5R-ABT | ETM-10R-ABT | ETM-15R-ABT | ETM-20R-ABT | ETM-30R-ABT | ETM-45S-ABT | ETM-60S-ABT |
---|---|---|---|---|---|---|---|
Shape | Round (cylinder) | Round (cylinder) | Round (cylinder) | Round (cylinder) | Round (cylinder) | Square (cubic) | Square (cubic) |
Stacking Capacity | 4.6cbm | 9.802cbm | 15.08cbm | 20.358cbm | 31.104cbm | 45.36cbm | 62.208cbm |
Stacking Size (mm) | 3200 *1200*1200 | 5200*1300*1450 | 8000*1300*1450 | 10800*1300*1450 | 10800*1600*1800 | 10800*2100*2000 | 10800*2400*2400 |
No.s of Fan Motors | 3 | 4 | 6 | 8 | 10 | 8 | 8 |
Power Required | 35kw | 40kw | 55kw | 75kw | 120kw | 155kw | 165kw |
Steam Volume | 10kg/h | 13kg/h | 13kg/h | 17kg/h | 25kg/h | 25kg/h | 34kg/h |
Container Required | 20GP | 20GP | 40HC | 40HC | 40FR | 40FR | 40FR |
Loading Method | End-opening rail type | ||||||
Heating Medium | Electric heating thermal oil (Thermal oil boiler type can be custom made) | ||||||
Equipment Body | Inner layer: stainless steel; external layer: steel reinforcement; aluminum silicate and rock wool combination insulation layer; external high-quality metal packaging. | ||||||
Control System | Automatic controller (HMI screen, PLC, remote control supported); temperature sensor module combination system; pressure sensor module combination system; power distribution cabinet and its electrical components, etc. | ||||||
Heating circulation system | Motor; aluminum alloy fan; active shaft and accessory parts; electric heater; piping, etc. | ||||||
Humidification system | Stainless steel steam spray pipe; valve; solenoid valve. | ||||||
Cooling system | Blower; electric valve. | ||||||
Automatic inlet and outlet system | Loading trolley; kiln outside inlet and outlet tracks; electric transport control device | ||||||
Automatic drainage system | Electric valves; piping and water release devices. |
All thermal modification kilns can be custom made as per customer’s requirement.